Case study 1
„TOOL LIFE 26M PER ACTIVE HOB TOOTH, 17’000 PARTS PRODUCED PER RESHARPENING"
Application
Car Gear Box ManufacturingCustomer request
Reduction of cost per part maintaining the same cycle time, dry finish hobbing before heat treatment, in DIN quality class 7Suggested solution by Schnyder
Replacement of PM steel hob with solid carbide nanograin hob.Component / tool
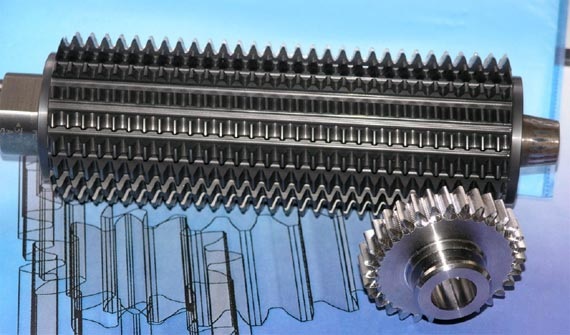
Component / gear data
31 tooth spur gear, DP12 (M2.1167) – 20° PA, external Ø70.3mm, useful length 17mm, material 16MnCr5 with 630 N/mm2Hob specification
Shank type gear hob: Ø80 x 273/ 200 – shank Ø32/ SK30 - 19 gashes, Nanograin solid carbide (AAA) / 2 RHSCoating: Alcrona
Process
First cut: h 4.60mm in climb cutting vc 280 m/min. / fa 1.80 mm/RSecond cut: h 5.125mm conventianal cutting vc 400 m/min. / fa 1.20 mm/R
chip thickness ca. 0.10- 0.13mm
Hobbing machine
Pfauter P210 CNCResult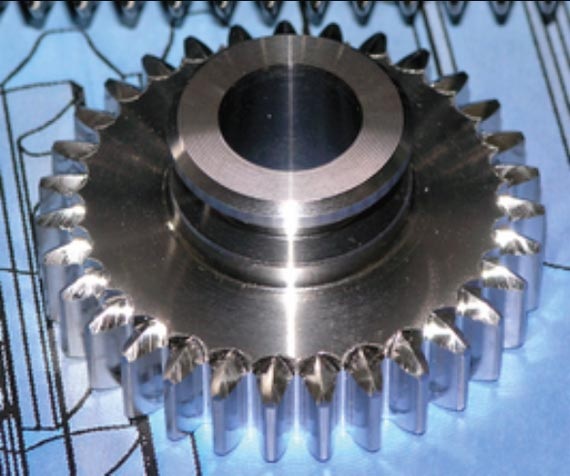
# of parts produced per resharpening: 17‘000 pcs (!) # of resharpenings: 25
Total cutting length: 151‘000 m
Chip volume: 6‘300 mm3/piece
Total # of hob teeth: 285
# of active hob teeth: 238
Tool life: 26 m / active hob tooth
Achieved gear quality with new hob
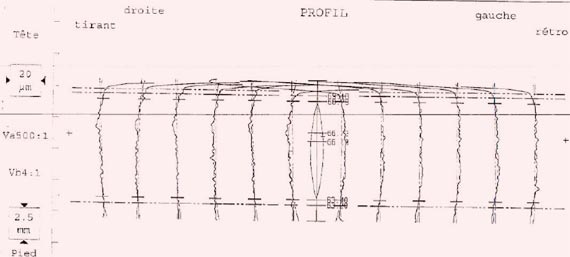
Achieved gear quality after 13'000 parts (wear of 0.05mm)
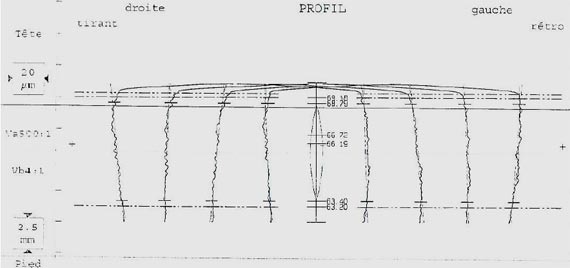
Customer benefit
Tool life of PM steel hob: 2'000 parts per resharpening.Achieved tool life with Schnyder solid carbide hob: 17'000 parts per resharpening.
Benefit:


Case study 2
„TOOL LIFE 26M PER ACTIVE HOB TOOTH, 17’000 PARTS PRODUCED PER RESHARPENING“
Application
Car Steering System ManufacturingCustomer request
Reduction of cost per part maintaining the same cycle time, dry finish hobbing before heat treatment, in DIN quality class 7Suggested solution by Schnyder
Solid carbide shank hob type PERFECT CUT®Component / tool
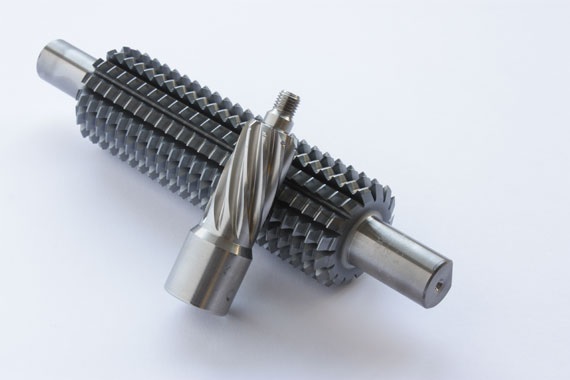
Component / gear data
9 tooth helical pinion, Mn 2.00 – 25° PA, external Ø24mm, useful length 45mm, material 16MnCr5 with 630 N/mm2Hob specification
Shank type gear hob: Ø50 x 233/ 153 – shank Ø22 (2x) - 15 gashes, Nanograin solid carbide (AAA) / 1 LHSCoating: Alcrona
Process
First cut: h 3.16mm; in climb cutting vc 375 m/min. / fa 1.50 mm/RSecond cut: h 3.46mm; conventianal cutting vc 400 m/min. / fa 1.20 mm/R
chip thickness ca. 0.16mm
Hobbing machine
Gleason Pfauter P60 CNCResult
# of parts produced per resharpening: 44‘000 pcs (!)# of resharpenings: 24
Total cutting length: 440‘000 m
Chip volume: 5'042 mm3/piece
Total # of hob teeth: 349
# of active hob teeth: 296
Tool life: 65 m / active hob tooth
Achieved gear quality with new hob
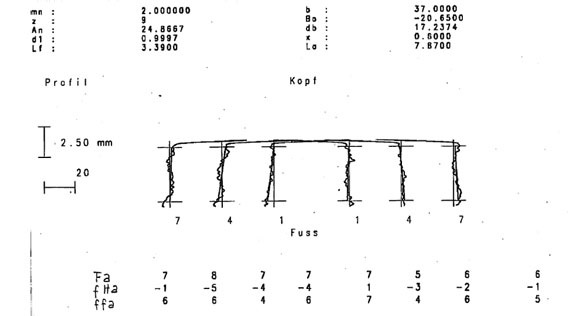
Achieved gear quality after 44'000 parts (wear of 0.1mm)
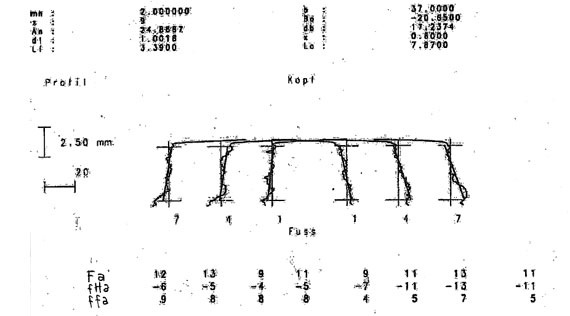
Customer benefit
Tool life of standard hob: 12'000 parts per resharpening.Achieved tool life with Schnyder PERFECuT® hob: 44'000 parts per resharpening.
Benefit:

